laser welder gun uses a high-energy laser beam as a heat source. The laser generates a high-energy-density laser beam and focuses the beam on the workpiece through a focusing lens. The heat generated by the interaction of the laser with the material causes the material to locally melt and join together. While melting, the laser beam continues to act, causing the molten metal to solidify under pressure to form a weld. This technology is not only efficient but also enables precise control.
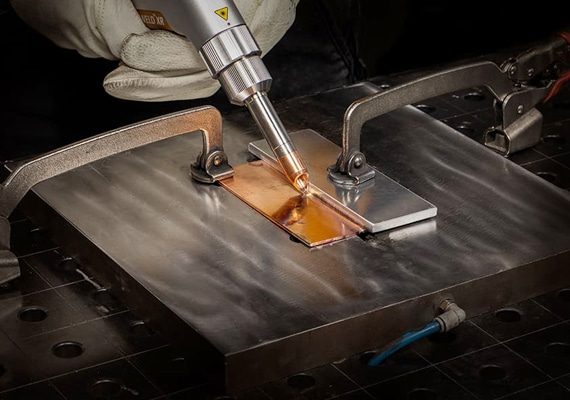
Laser Welding Machines for Metal
Laser welding machine, or laser beam welding machine, is a new type of welding method using laser technology. The laser welding machine can realize welding processes such as spot welding, butt welding, overlap welding, and sealing welding for thin materials.They are widely used to welding carbon steel, stainless steel, aluminum and is unlikely to be restricted by the workpiece shapes.
This laser beam welding method has the advantages of small welding seam width, small heat-affected zone, small deformation, fast welding speed, smooth welding seam, and high welding seam quality. The welded parts require no or little further treatment, which is conducive to the manufacturing of other equipment or machinery.
The hot-sale laser power outputs are 1.5kW and 3kW, and of course you can choose 3kW laser if you need to weld deeper. The higher the laser power, the greater the welding thickness and the faster the welding speed.
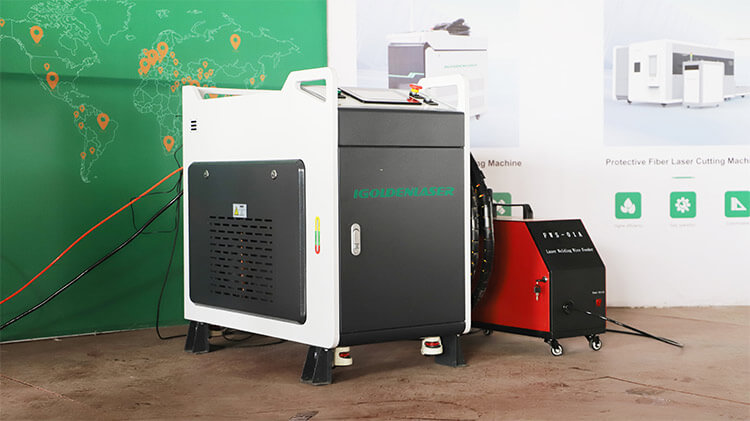
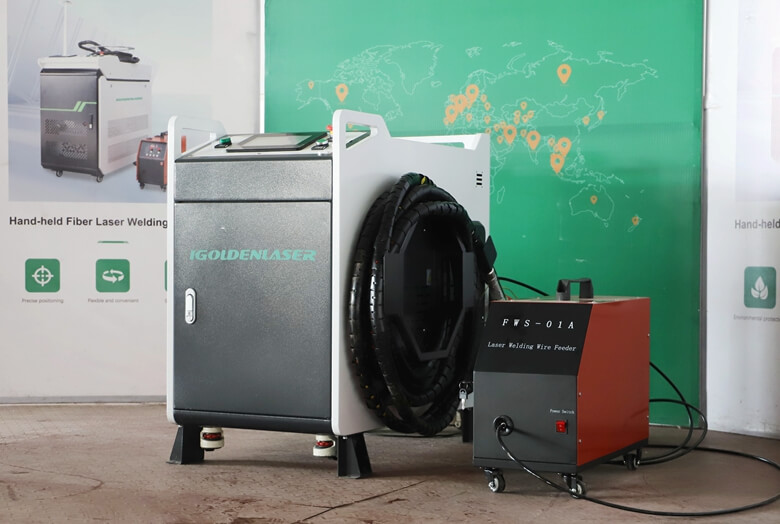
- Laser Source: The process begins with a laser source, which can be of different types such as solid – state lasers (e.g., Nd:YAG – Neodymium – doped Yttrium Aluminum Garnet), fiber lasers, or diode lasers. The laser source emits a high – intensity beam of coherent light. For example, fiber lasers are known for their high beam quality and energy efficiency, making them a popular choice in many industrial applications.
- Beam Delivery System: The laser beam is then directed through a beam delivery system. This typically consists of mirrors and lenses that focus and guide the beam to the welding area. The focusing of the beam is crucial as it determines the energy density at the workpiece. A well – focused beam can achieve a very high energy density, which is necessary for efficient material melting.
- Absorption of Laser Energy: When the laser beam reaches the workpiece, the material absorbs the laser energy. The absorption rate depends on various factors such as the material’s optical properties, the laser wavelength, and the surface condition of the material. For example, metals generally have a high absorption rate for certain laser wavelengths, while non – metals may require different laser settings to achieve effective energy absorption.
- Melting and Fusion: As the material absorbs the laser energy, it heats up and reaches its melting point. The molten pool is formed at the joint interface, and the laser beam continues to supply energy to maintain the molten state. The two parts being welded then fuse together as the molten material solidifies. The welding speed and the power of the laser beam can be adjusted to control the size and shape of the molten pool and the quality of the weld.
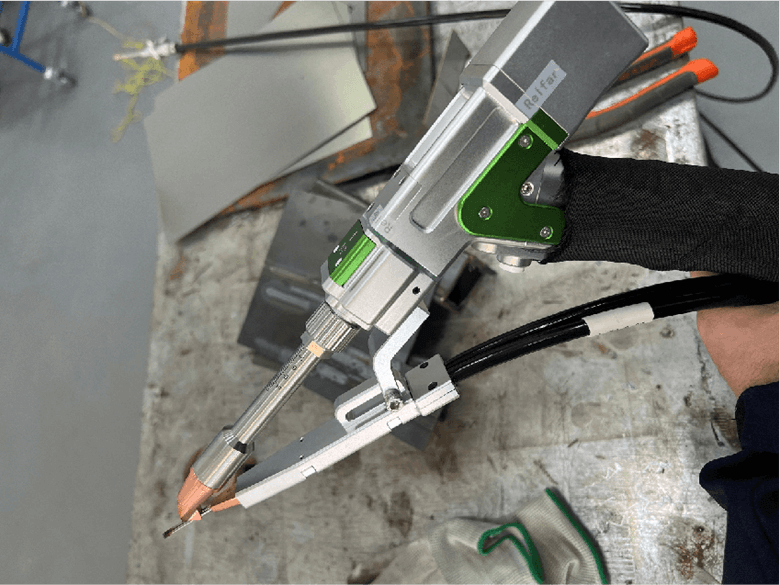
Power Requirements And Greatest Thickness Of Common Welding Materials
For different thicknesses of materials, the power requirements of laser welding machines vary. Generally speaking, laser welding thickness is directly proportional to the laser power.
The melting point and thermal conductivity of different materials will also affect the effect of laser welding. Materials with low melting points and high thermal conductivity must lower laser power and faster welding speeds. The opposite is true for materials with high melting points and low thermal conductivity.
Welding of highly reflective materials may require higher laser power. Such as Aluminum laser welding and copper laser welding.
Laser welding machine welding capability table
|
Laser power |
1000W |
1500W |
2000W |
3000W |
Carbon steel |
3mm |
4mm |
5mm |
8mm |
Stainless steel |
3mm |
4mm |
5mm |
8mm |
Galvanized sheet |
3mm |
4mm |
5mm |
8mm |
Aluminum |
1mm |
2mm |
3mm |
6mm |
Applicable materials |
Thin metal sheets, small precision parts |
Thin metal sheets, small precision parts |
Medium thickness metal plate suitable for most industrial applications |
Thick metal plate, suitable for mass production and heavy industry |
Laser Welding History
Early Laser Welding Technology
The story of laser welding began with the development of the first laser in the 1960s. Initially, laser technology was more theoretical and had limited practical applications. The first practical application of lasers for welding was the development of CO2 lasers. These early systems were large, expensive, and limited in power. Yet they also demonstrated the potential of laser welding in industrial settings. Initial experiments focused on simple welds of metals and other materials, showing that lasers could achieve precise, clean welds with minimal heat-affected zones.
Technological Advancements
Laser welding technology has made significant advances over the decades. The introduction of the fiber laser marked a major milestone. It offers better beam quality, higher efficiency, and greater flexibility. Unlike its predecessors, fiber lasers use optical fibers to generate and send the laser beam. This allows for more precise control and higher power levels. Also, the development of neodymium lasers has led to higher peak powers and the ability to operate in pulsed mode. This is ideal for specific applications such as deep penetration welding and drilling.
These technological advances have led to the miniaturization of laser welding systems. Modern systems are more compact, more energy-efficient, and can be integrated into automated production lines.
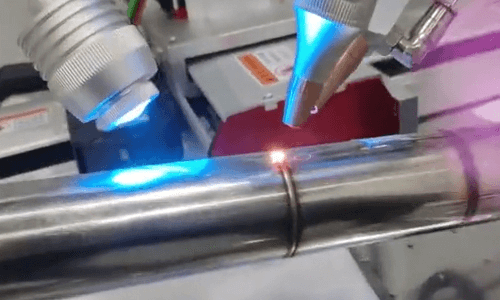
Modern Applications of Laser Welding Machines
Today, laser welding machines are indispensable in a variety of industrial applications. In the automotive industry, they can be used to weld car bodies, gear components, and battery packs. In the aerospace sector, laser welding ensures the structural integrity of critical components. The electronics industry can rely on laser welding to complete delicate tasks.
The versatility of modern laser welding machines makes them even more versatile. They can be used in industries where precision and cleanliness are critical, such as medical device manufacturing. Also, the continuous development of laser welding technology makes these machines more adaptable, efficient, and cost-effective.
Industrial Manufacturing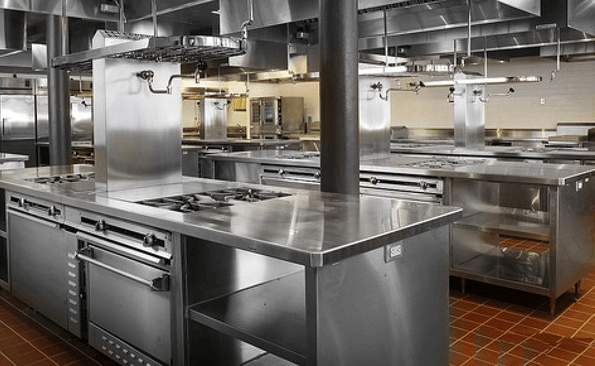
Laser welding machines are widely used in industrial manufacturing. In the automotive industry, laser welding is used to assemble car bodies, electric vehicle batteries, and even precision components such as sensors. It is able to produce consistent, high-quality welds at high speeds. This makes laser welding key to meeting the needs of large-scale production. In aerospace manufacturing, laser welding ensures that components are connected accurately and reliably. High strength and minimal deformation are essential to maintain the integrity and performance of the system.
In the electronics industry, laser welding is used to join small, delicate components. Examples include connectors, circuit boards, and battery packs. The precision of laser welding minimizes the risk of damaging sensitive components. This capability is particularly important in the production of consumer electronics, medical devices, and telecommunications equipment.
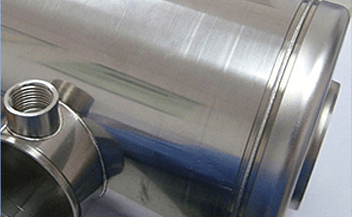
Special Applications
Laser welding machines are also used in applications that need high precision and cleanliness. Medical device laser welding joins small, complex components in surgical instruments, implants, and other medical devices. The precision and control of laser welding do not compromise their biocompatibility or structural integrity.
Laser welding machines are also used in applications that need high precision and cleanliness. Laser welding medical devices join surgical instruments, implants, or small, complex parts. The precision and control of laser welding do not compromise their biocompatibility or structural integrity.
- High – Precision Welding: Laser welding offers exceptional precision, capable of achieving weld widths as small as a few tenths of a millimeter. This precision is crucial in industries where small and intricate components need to be joined, such as in electronics and medical device manufacturing. For example, in the production of pacemakers, laser welding is used to join tiny electrical leads and components with high accuracy to ensure the proper functioning of the device.
- Minimal Distortion: The concentrated heat input from the laser beam results in a relatively small heat – affected zone. This means that the surrounding material is less affected by the welding process, reducing the risk of warping and distortion. In the aerospace industry, this is of great importance when welding components made of lightweight alloys, as any distortion can affect the performance and safety of the aircraft.
- Efficient Production: Laser welding can be a very fast process, especially when using high – power lasers and appropriate welding parameters. The rapid melting and solidification of the material allow for quick welds, increasing production efficiency. In the automotive manufacturing process, laser welding can significantly reduce the time required to assemble vehicle components compared to traditional welding methods.
- Automation Compatibility: The precision and speed of laser welding make it highly suitable for automation. It can be integrated with robotic systems and computer – numerical – control (CNC) machines to perform complex and repetitive welding tasks with high accuracy and consistency. This enables manufacturers to achieve high – volume production with excellent quality control.
- Wide Range of Materials: Laser welding can handle a diverse range of materials, including various metals such as steel, aluminum, titanium, and copper, as well as some non – metals and composites. Different laser types and welding parameters can be adjusted to suit the specific properties of each material. For example, fiber lasers are often used for welding metals, while other laser types may be more suitable for non – metals or specific alloy combinations.
- Dissimilar Material Welding: It is also capable of welding dissimilar materials together. This is particularly useful in industries where the combination of different materials is required to achieve specific properties, such as in the manufacturing of electronic components with different conductive and non – conductive materials or in the production of hybrid structures in the automotive and aerospace industries.
- Reduced Tool Wear: As a non – contact welding method, laser welding eliminates the need for physical contact between the welding tool and the workpiece. This reduces the wear and tear on the welding equipment, resulting in lower maintenance costs and longer tool life. In contrast, traditional welding methods such as arc welding can cause electrode wear and require frequent replacement of welding tips.
- Access to Confined Spaces: The non – contact nature of laser welding allows for welding in hard – to – reach or confined spaces. The laser beam can be precisely directed to the welding area without the need for physical access with a welding tool. This is advantageous in the assembly of complex mechanical systems or in the repair of small and intricate components.
IGOLDEN BLOG
Thank you for visiting the iGOLDENCNC website. iGOLDENCNC is the professional supplier of CNC machinery application solution, within the business of producing and selling CNC machinery and accessories.