The automatic laser welding machine includes X, Y, Z axis linear motion and R axis rotary motion to realize the linear or curved motion of the welding space and the welding angle adjustment of the welding torch to the workpiece, thereby completing the welding of various special-shaped welds. The X, Y, and Z axis motion systems are driven by AC servo motors, driven by ball screws and guided by guide rails to achieve precise control of walking. It can manually adjust and control the welding angle adjustment requirements of the welding gun and the workpiece, and cooperate with the X, Y, and Z axes to achieve the completion of the welding process.
This is an automatic laser welding machine, which is mainly suitable for mass production. And it can realize spot welding, butt welding, overlap welding, sealing welding and other welding processes for thin-walled materials and precision parts. It has the advantages of wide application range, high precision and fast speed.
360° Welding
It can achieve automatic or semi-automatic electric welding, with aesthetically pleasing and strong welds, fast speed, no consumables, minimal workpiece deformation, and no need for post-welding grinding.
CNC three-axis moving table (XYZ)
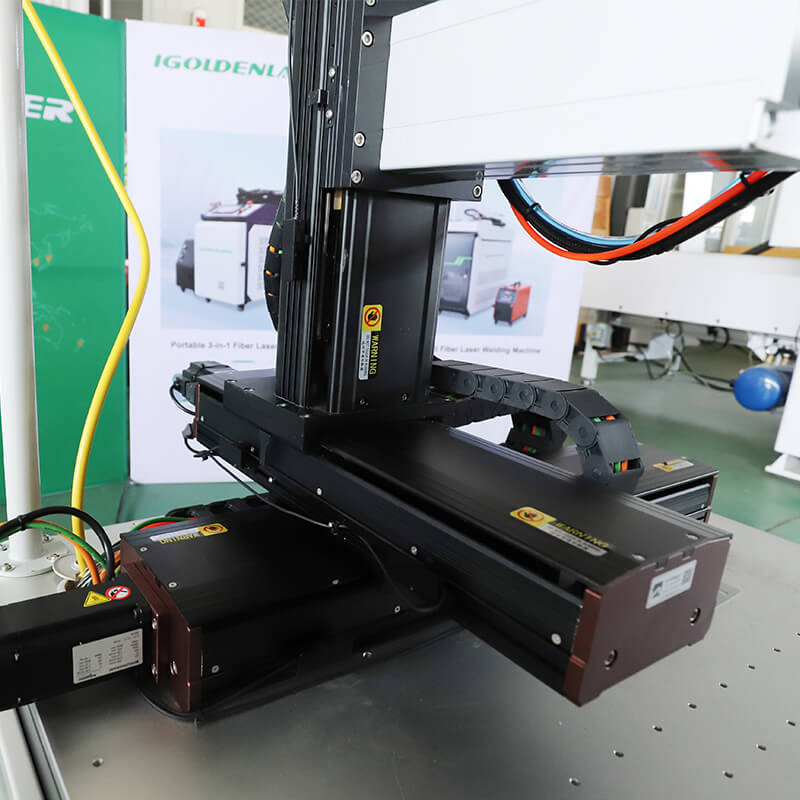
Feature Of Laser Welder with Plateform Automatic
- Laser Welding Technology: Laser welding utilizes a high-energy laser beam to melt and fuse materials together. The laser beam is focused on the welding area, creating a concentrated heat source that causes the materials to melt and form a strong bond upon cooling. Laser welding offers several advantages, including precise control, minimal heat-affected zone, high welding speed, and the ability to weld complex geometries.
- Fully Automatic Operation: A platform fully automatic laser welding machine is designed for automated operation. It incorporates advanced robotics and motion control systems to manipulate the workpieces, position them accurately, and execute the welding process without human intervention. This automation enables continuous and efficient production with minimal downtime.
- Platform Design: The “platform” in the machine’s name refers to a stable and versatile work surface or workspace where the welding operations take place. The platform provides a controlled environment for positioning and securing the workpieces, ensuring stability and accuracy during the welding process. The design of the platform may vary depending on the specific machine model and manufacturer.
- Integration and Control Systems: A platform fully automatic laser welding machine integrates various components and systems to ensure seamless operation. This typically includes laser sources, robotic arms, workpiece fixtures, sensors, vision systems, safety features, and a control unit. The control unit manages the machine’s operations, programming, and monitoring, allowing for precise control of welding parameters and process parameters.
- Applications: Platform fully automatic laser welding machines are used in a wide range of industries and applications. They are particularly suitable for welding small to medium-sized components or parts with high precision requirements. Examples of applications include automotive manufacturing, aerospace, electronics, medical devices, jewelry production, and precision engineering.
- High Welding Speed and Efficiency: Laser welding machine offer high welding speeds, which significantly improves overall production efficiency. The automated nature of the machine ensures continuous operation, reducing the need for manual intervention and minimizing production downtime. This makes it ideal for high-volume production environments.
- Quality and Precision: Laser welding provides excellent welding quality and precision. The focused laser beam allows for precise control over the heat input, resulting in minimal distortion, precise weld seams, and strong weld joints. The automation aspect of the machine ensures consistency and repeatability, leading to reliable and high-quality welds.
Automated Laser Welding Machine Application
An automated laser welding machine with CNC controller is mainly used in cell phone batteries, jewelry, electronic components, sensors, watches, precision machinery, communications, handicrafts, high-end cabinets, elevator accessories, stainless steel door handles, high-end furniture, stainless steel hip flasks and other industries.
An automatic laser welder can realize laser welding between carbon steel, alloy steel, stainless steel and other different steels, as well as stainless steel-nickel alloy, nickel electrode-cold forged steel, bimetallic strips with different nickel content, titanium, nickel, tin, copper, aluminum, Welding between chromium, niobium, gold, silver and other metals and their alloy materials. In addition, it can also realize the welding between copper-nickel, nickel-titanium, copper-titanium, titanium-molybdenum, brass-copper, carbon steel-copper and other dissimilar metals.
IGOLDEN BLOG
Thank you for visiting the iGOLDENCNC website. iGOLDENCNC is the professional supplier of CNC machinery application solution, within the business of producing and selling CNC machinery and accessories.