IIGCL-MOPA(100w-500w)
Pulse Laser Cleaning Machine
Laser cleaning machine is a new generation of high-tech products used for surface cleaning, can effectively remove the surface adhesion or surface coating of the cleaned object at high speed, so as to achieve a clean process.
The use of high frequency high energy laser pulse irradiate the workpiece surface, make the surface oil, rust or coating instantaneous evaporation or stripping, high-speed and effective cleaning object surface attachment or surface coating, so as to achieve a clean cleaning object process.
It is characterized by no damage to the parts matrix, no consumables, energy saving and environmental protection, to meet the requirements of complex modeling and fine positioning in the field of industrial processing, to achieve a higher cleaning effect and a lower overall cost of production benefits.
Advantages of Pulse Fiber Laser Cleaning Machine
- Non-contact cleaning, do not damage parts matrix;
- Precision cleaning, can realize the precise location, accurate size selective cleaning; High cleaning efficiency, save time; u
- Don’t need to use any chemicals and cleaning fluid, basic for solid waste powder after cleaning, small volume, easy to store, can easily solve the problem of chemical cleaning;
- Simple operation, can be hand-held or cooperate with manipulator automation cleaning;
- Of human body engineering design, the operation labor intensity is greatly reduced;
- Laser cleaning system is stable and almost no maintenance;
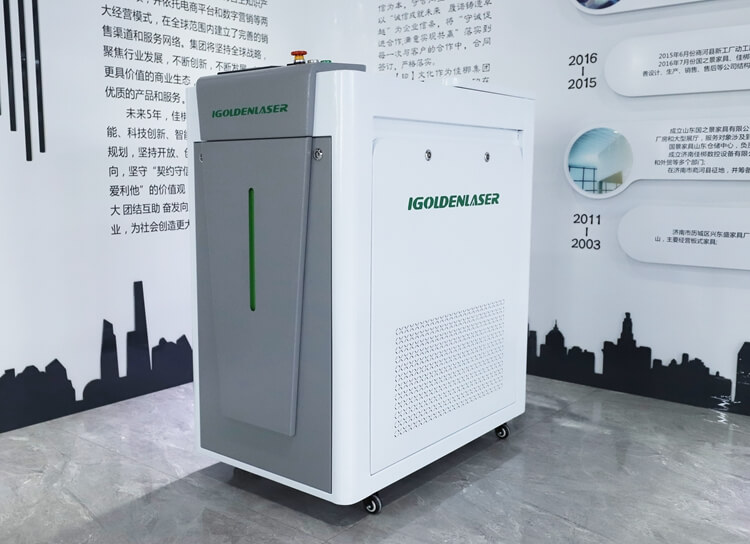
TECHNICAL PARAMETER
Service voltage | Single-phase 220V±10%, 50/60Hz AC |
Overall power consumption | <4800W |
Operating temperature | 5℃~40℃ |
Operating humidity | ≤80% |
Laser power | 100W-500W |
Laser power instability | <2% |
Laser type | Pulse |
Pulse width | 2-500ns adjustable |
Max. monopulse energy | 2mJ |
Optical quality(M2) | <1.8 |
Controlling power range(%) | 0-100(Gradient adjustable) |
Frequency adjustment range(kHz) | 1-4000kHz(Gradient adjustable) |
Fiber length | 5m |
Type of cooling | 100W/200W air-cooled, 300W/500W water-cooled |
Scanned area | 0.01~350mm |
Scanning speed | 0~60000mm/s |
Field lens focal length(mm) | 240mm |
Cleaning mode | 8 kinds |
Machine size (L*W*H) | 1107mm*660mm*1061mm |
Total weight | 165KG |
Cleaning head weight | 1.4KG |
Operating mode | Handheld |
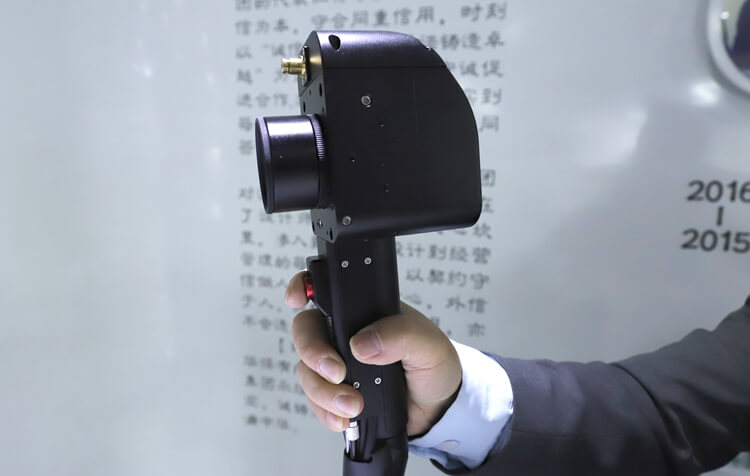
Hand cleaning head(Water cooling)
Small and light, different cleaning modes, multi-system compatible.
Hand cleaning head(Air cooling)
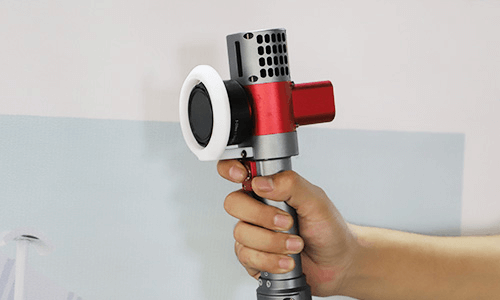
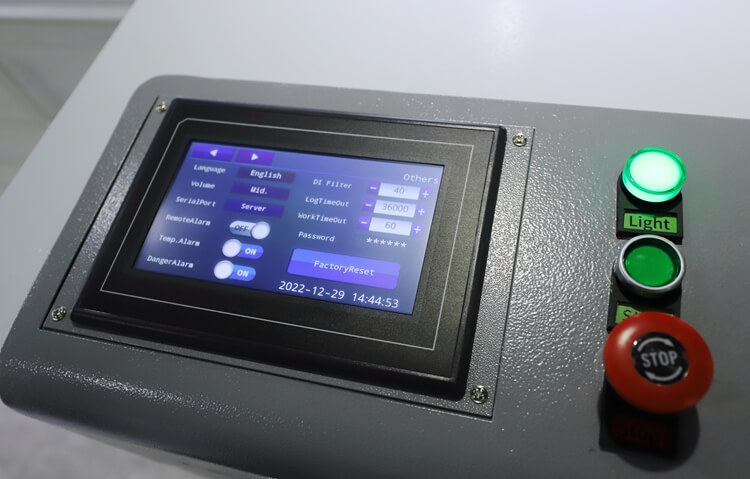
Touch screen panel
Friendly interface; Rich functions, a variety of cleaning modes are optional, easy to learn.
Hanli/S&A water chiller
1. The cooling capacity is up to 1400W, and environmentally friendly refrigerants can be used;
2. The temperature control accuracy can reach ±0.3C°;
3. The intelligent thermostat has two temperature control modes, which are suitable for different use occasions; it has a variety of settings and fault display functions;
4. With multiple alarm protection functions.
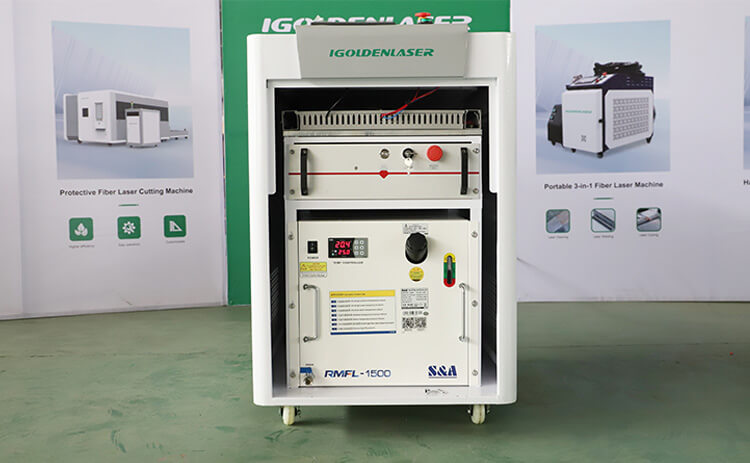
Handheld Laser Cleaning Machine for Removing Rust, Stains, Paint
> Rust removal on metal surface;;> Surface paint removal treatment;
> Surface resin, oil, stains, dirt cleaning;;> Surface coating, coating removal;
>Pretreatment of welding surface/spraying surface; > Removal of dust and attachments on the surface of stone statues;
> Rubber mold residue cleaning.
Pulse Laser Cleaning Machine Buyer Guide
Pulse laser cleaning machine uses pulsed laser energy to scanning the surface of metals, removing contaminants, rust, and oxides through physical reactions.
How does a pulsed laser work? The working principle of a pulsed laser cleaning machine involves the laser beam emitted by the laser being absorbed by the contamination layer on the surface. By adjusting the laser’s energy density, the dirt heats up and expands. When the expansion force exceeds the adhesion between the dirt and the base material, the dirt detaches from the surface. To prevent surface damage, the laser pulse width must be short enough to avoid heat buildup.
Additionally, the laser beam’s low divergence angle and excellent directionality allow it to be focused into different spot sizes using a focusing system. At high energy absorption, a rapidly expanding plasma is formed, generating shock waves that further assist in removing contaminants.
Compared to traditional cleaning methods, pulse laser cleaning machines can adjust laser parameters for different types of dirt, removing various stains without damaging the surface and preserving the material’s original appearance and performance.
educed Thermal Effects:
Pulsed laser cleaning uses short laser pulses, with each pulse lasting for a very brief time. This means the heat is quickly removed before it can spread to the surrounding material, minimizing thermal damage to the substrate—especially important for heat-sensitive materials.
Higher Energy Efficiency:
Pulsed lasers concentrate their energy release in a short time, leading to higher energy efficiency. In contrast, continuous-wave lasers may cause energy accumulation on the material surface over extended exposure, increasing the damage risk of base material.
Better Selectivity:
Pulsed lasers allow for adjustable pulse width and energy density based on the type of contaminants, achieving optimal cleaning results. Continuous-wave lasers have a more limited range of parameter adjustments, making fine-tuned selective control more challenging.
Stronger Shock Wave Effect:
High-energy pulsed lasers can instantly generate plasma, creating strong shock waves that help remove stubborn contaminants. In comparison, the plasma effect generated by continuous-wave lasers is relatively weaker.
Higher Cleaning Efficiency:
Pulsed laser cleaning can complete tasks in a shorter time, particularly effective for removing thin-layer contaminants. Continuous-wave lasers may require longer durations to achieve similar cleaning results.
Two Types of Pulsed Lasers
In laser cleaning applications, two main types of lasers are widely used: Q-switched pulsed lasers and ultrashort pulsed lasers.
Q-Switched Pulsed Lasers
Q-switched pulsed lasers generate short pulses by abruptly releasing the energy stored within the laser resonator. These pulses are typically in the nanosecond range (10^ (-9)) seconds.
Key features of Q-switched pulsed lasers include:
High Pulse Energy:
Each pulse delivers relatively high energy, making it effective for removing thicker or harder contaminants.
Longer Pulse Width:
Although their pulse width is longer than that of ultrashort pulsed lasers, nanosecond pulses can still create sufficient transient heating to remove contaminants effectively.
Cost-Effectiveness:
Q-switched pulsed lasers are generally less expensive than ultrashort pulsed lasers, making them a more economical choice in many cases.
Versatility:
Suitable for cleaning a wide range of materials, including metals, plastics, and ceramics.
Ultrashort Pulsed Lasers
Ultrashort pulsed lasers produce pulses in the picosecond (10^ (-12)) seconds) or femtosecond (10^ (-15)) seconds) range.
Key features of ultrashort pulsed lasers include:
Extremely Short Pulse Width:
The very brief pulse duration prevents heat from spreading to surrounding materials, concentrating energy solely on the contaminant.
Low Thermal Effect:
Due to their extremely short pulse width, the impact on the substrate is minimal, making them ideal for cleaning heat-sensitive materials.
High Precision:
Capable of extremely precise surface treatment, suitable for applications requiring high-precision cleaning.
Strong Selectivity:
Allows for the precise removal of specific contaminants without damaging the substrate.
Compared with continuous laser cleaning, pulsed laser cleaning machine has more advantages, but its biggest disadvantage is that the price is very expensive, which exceeds the purchase budget of many enterprises.
The price of a laser cleaning machine ranges from several thousand dollars to tens of thousands of dollars, and the specific price is affected by many factors.
Pulsed lasers emit high-energy laser beams in an extremely short time, offering exceptionally high peak power and instantaneous power density. Unlike continuous wave lasers, high-power pulsed lasers can generate intense heat in an instant, but because the duration is so brief, the heat doesn’t have time to spread to the surrounding material. This significantly reduces the thermal impact on the substrate. High-power pulsed lasers also allow for precise control of the cleaning process by adjusting the pulse energy and frequency. This adjustability enables customization for different cleaning requirements, ensuring compatibility with various materials and application scenarios.
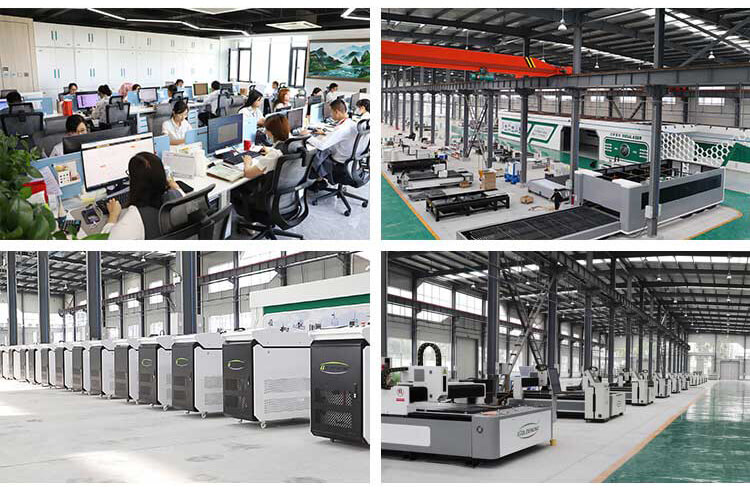